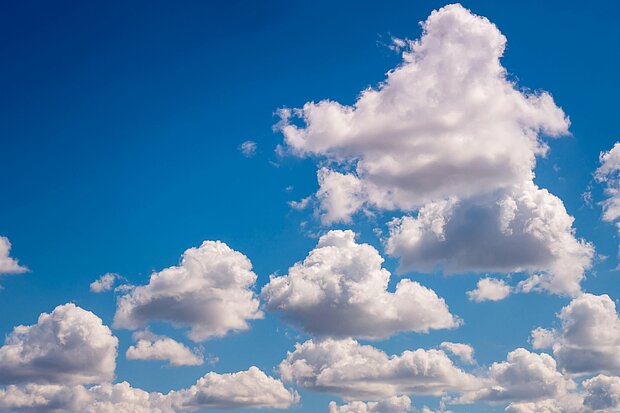
AndonCloud
AndonCloud reduziert Ausfallzeiten und rationalisiert den Informationsfluss für eine Fertigungsanlage. Es hilft auch, Geld zu sparen, indem es die Verzögerung zwischen der Änderung des Status der Maschine und dem Aufruf der entsprechenden Dienste zur Reparatur minimiert.
Branche: Produktion
Kunde: Ein amerikanischer Mischkonzern
Der amerikanische Mischkonzern, der in der Maschinen- und Anlagenproduktion, der Energieerzeugung und der Ölindustrie stark vertreten ist, zählt zu den größten Unternehmen der Welt. Das Unternehmen trat in den 1990er Jahren in den polnischen Markt ein und betreibt heute acht Produktionsstätten, in denen 7.300 Mitarbeiter beschäftigt sind. Bei unserem Kunden handelt es sich um ein Werk zur Herstellung von Generatoren.
Sie haben Fragen oder wünschen sich eine persönliche Beratung?
Wir sind gerne für Sie da. Nehmen Sie über unser Kontaktformular oder telefonisch Kontakt zu uns auf.